How to Avoid Costly Equipment Failures Before They Happen
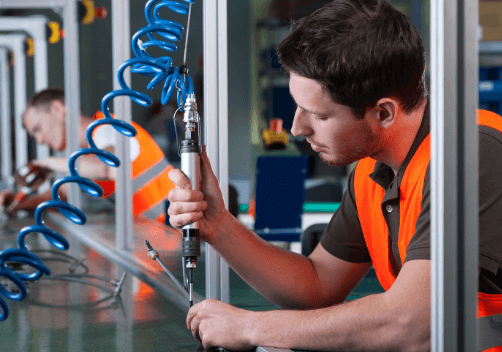
Equipment breakdowns rarely happen out of nowhere. In most cases, there were warning signs—small flaws or hidden cracks—that went unnoticed until it was too late. And by the time something fails, the cost isn’t just about replacing a part. Downtime, safety risks, production delays, and unexpected repairs can quickly snowball into a major issue. Fortunately, many of these failures are entirely preventable with the right inspections in place. Tools like magnetic particle inspection allow teams to detect surface and near-surface flaws in metal components before they cause real damage.
Whether you’re maintaining industrial machinery, infrastructure, or critical transport parts, prevention is your most cost-effective strategy. Waiting until something breaks might seem like you’re “saving money for now,” but in reality, proactive maintenance almost always costs less in the long run.
So how do you spot the early signs of failure—before they become major problems? It starts with a better understanding of your equipment, your inspection tools, and the patterns that typically lead to wear and failure.
What Really Causes Equipment Failure?
Mechanical failure doesn’t happen in a vacuum. It’s often the result of gradual wear and tear, minor defects that go undetected, or environmental stress that builds over time. Here are some of the most common culprits:
- Fatigue cracks: Repeated stress or vibration can cause small cracks in metal parts, especially welds or joints.
- Corrosion: Exposure to moisture, chemicals, or salt can weaken surfaces and compromise their integrity.
- Improper installation: Misaligned components or incorrect torque settings can place unexpected stress on parts.
- Lack of routine inspection: If flaws aren’t identified early, they have time to grow, often invisibly, until a failure occurs.
Most of these issues are hard to see with the naked eye—which is why specialised inspection methods are essential.
See also: Technology Integration in Architecture: Insights from Keystone Architects
The Power of Non-Destructive Testing (NDT)
Non-destructive testing (NDT) refers to a group of inspection techniques that evaluate the condition of materials or components without damaging them. These methods are widely used in industries like manufacturing, construction, mining, and aviation, where safety and reliability are critical.
Magnetic particle inspection (MPI) is a type of NDT used specifically for detecting surface and slightly subsurface cracks in ferromagnetic materials. It works by magnetising the part and applying fine iron particles to the surface. If there’s a flaw, the particles gather around it—revealing the defect clearly and precisely.
This method is especially useful for:
- Weld inspections
- Shafts, gears, and bearings
- Pressure vessels and pipelines
- Aircraft and automotive components
The process is quick, accurate, and doesn’t require disassembly, making it ideal for regular maintenance checks.
When and Where to Inspect
Knowing when to inspect is just as important as knowing how. While every piece of equipment is different, these are some smart times to schedule inspections:
- Before new equipment goes into service: This ensures it’s defect-free from the start.
- During scheduled maintenance windows: Don’t just change fluids—check for cracks or stress.
- After any heavy usage or unusual stress event: Overloads, impacts, or extreme conditions can create hidden flaws.
- Before critical production runs or projects: Ensure reliability before things ramp up.
Focus on high-stress areas and components that bear load, vibrate, rotate, or are exposed to the elements. These parts are most vulnerable to hidden damage that can lead to failure.
Prevention Saves More Than Money
Avoiding breakdowns is about more than just protecting the bottom line. Preventative inspections also improve:
- Safety: Fewer surprises mean less risk of injury or emergency situations.
- Efficiency: Well-maintained equipment runs smoother and more reliably.
- Reputation: Delays due to mechanical issues can hurt your credibility—especially in time-sensitive industries.
- Longevity: Spotting and fixing small issues early can extend the usable life of your assets.
It also builds trust with your team. When employees see that management takes maintenance seriously, they’re more likely to report early warning signs and follow procedures carefully.
Create a Culture of Proactive Maintenance
Preventing failure isn’t just about booking inspections—it’s about building habits. Here’s how to embed a proactive maintenance mindset across your team:
- Track inspection data: Keep a clear log of what’s been checked, when, and what was found.
- Train your team to spot visual signs: Oil leaks, misalignment, unusual vibrations—all these are clues.
- Standardise inspection intervals: Don’t wait for symptoms—make it routine.
- Partner with specialists: Use qualified inspectors who understand your equipment and industry.
When inspection becomes part of your operating rhythm—not an afterthought—you drastically reduce the risk of costly, inconvenient, and potentially dangerous equipment failures.
Stay Ahead, Not Behind
In business, waiting until something breaks rarely pays off. With tools like magnetic particle inspection and a proactive mindset, you can identify and solve problems while they’re still small. It’s a simple shift—from reacting to anticipating—that makes a massive difference to performance, safety, and cost. The smartest teams aren’t just fixing problems. They’re preventing them.